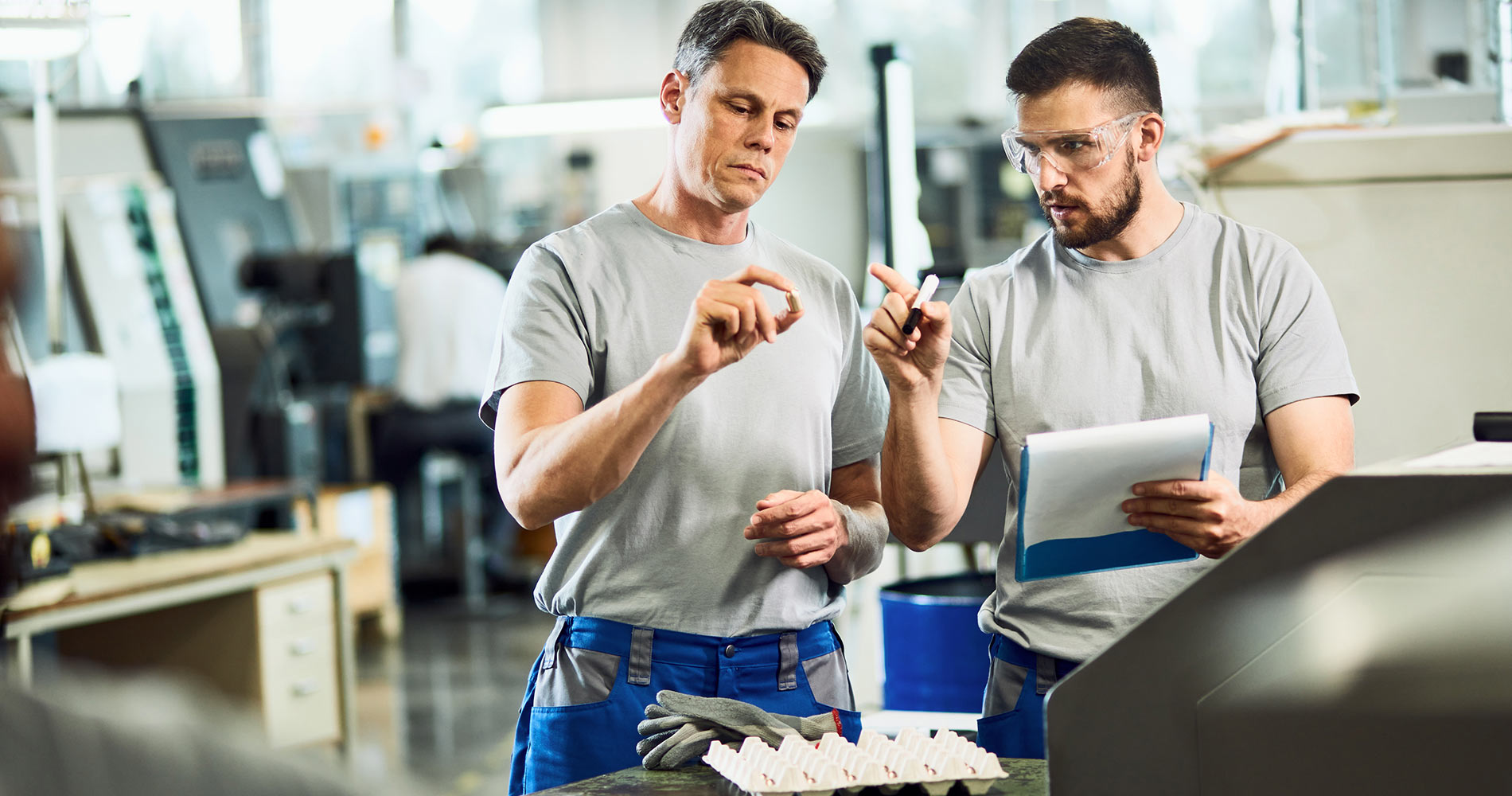
Let’s talk about Waste
Imagine you walk in to a bar and order a drink. The bartender takes your order and then proceeds to make your drink, however glasses are stored on one end of the bar, drinks are on the other and the card machine to pay is in use with another customer.
In terms of Lean Six Sigma, waste is anything that the customer does not value and is not prepared to pay for. Now, imagine a bar where glasses, drinks and paying tools are all within reach from a solitary point. This will reduce the time it takes to make a drink, to serve a thirsty customer and the waiting time for the next customer.
A foundation of the TPS (Toyota Production System) is to eradicate waste within the following 7 areas: Over inventory, Over Processing,Transportation, Motion, Rework, Overproduction and waiting.
We will use the bar example to detail these further.
- Over inventory: This waste refers to the waste produced by unprocessed inventory. Assets are held in stock, storage space is used, lighting within the warehouse etc. A bar may have lots of waste here as drink may be undrinkable within a certain timeframe.
- Over processing: Over processing occurs when employees are performing unnecessary processes or using the wrong tool for the job which can lead to defects.
- Transportation: This waste is moving materials from one point to another which adds no value to the end customer. For example the brewery should be based close to the outlets which sell the produce.
- Motion: Humans and machines can waste motion. When the bar tender has to move between glass, to drink, and spot to spot, they will lose energy and motion is wasted. Lean Six Sigma ensures everything that everything should be accessible to each person that needs it.
- Rework or defects: This waste is any deviation away from what the customer expects to receive. This has the most impact with the customers as quality and customer satisfaction are key components. In terms of a bar, this could be where a customer is given the wrong drink. This equates to waste of stock and reduction in customer experience.
- Over production: The most serious of all wastes as this can impact all other wastes in turn. Stocking too much of a product that goes unused has cost, storage, wasted materials and assets tied up in stock. Could you imagine a bar that pre-filled drinks before the customer had asked for their drink?
- Waiting: A waste due to halted production or poor management in customer planning. If a drinks order will take1 minute to place the order and pay for the product, and 1 minute to make the drink, time can be saved by working in pairs to make the drinks while one person deal with payment.
Want to know more about Lean Six Sigma, connect with Noon Edwards today to see how we can help you with your Lean Six Sigma journey.